ドリンク剤の製造工程とポイント
秤量・調製
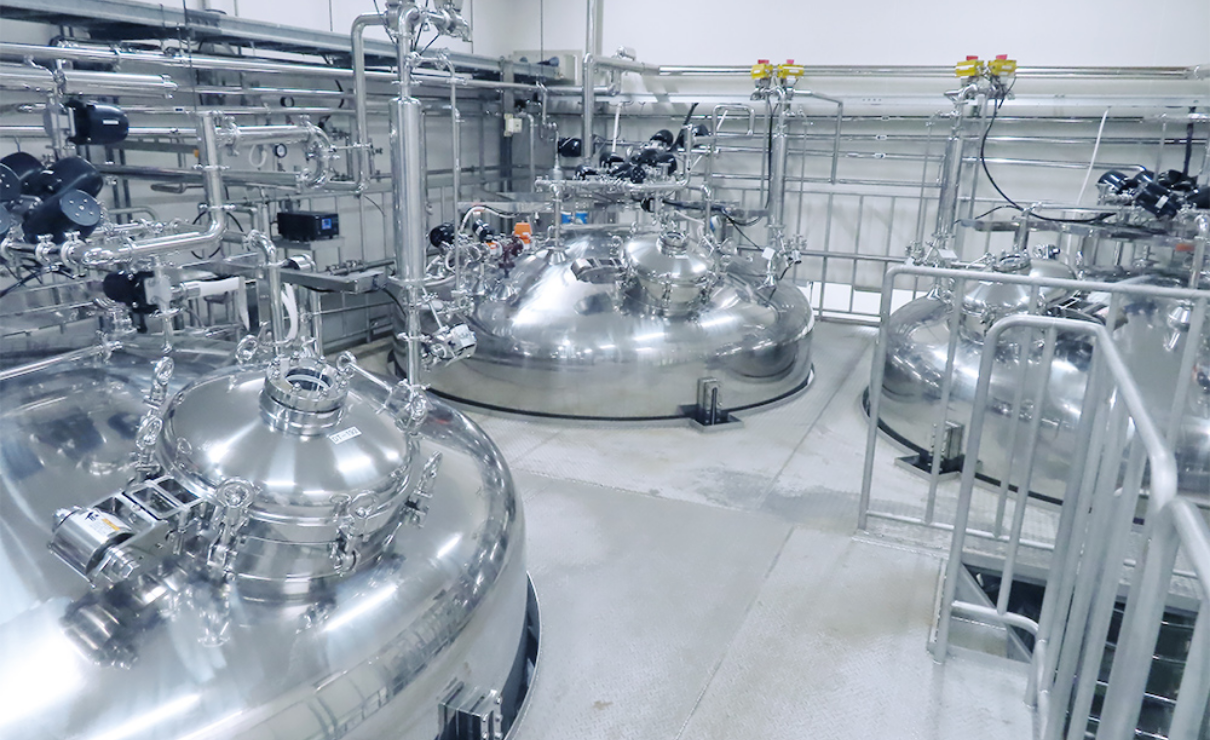
秤量作業は2名の作業員で行い、自動システムにより発行された製造指図記録書に基づき、指示された質量の原料をダブルチェックして計量します。
その後、秤量済みの各原料を検量し、異常が無いことを確認後に溶解槽で原料を溶解しながら、ポンプを介して調製タンクに順次送液します。
調製タンク(21,000L×3基+16,000L×2基)では薬液の撹拌混合を行い、全ての原料を投入後に薬液液量を調整後、調製済みの薬液をサンプリングして特性値を測定し、次工程の充填工程へ送液します。
その後、秤量済みの各原料を検量し、異常が無いことを確認後に溶解槽で原料を溶解しながら、ポンプを介して調製タンクに順次送液します。
調製タンク(21,000L×3基+16,000L×2基)では薬液の撹拌混合を行い、全ての原料を投入後に薬液液量を調整後、調製済みの薬液をサンプリングして特性値を測定し、次工程の充填工程へ送液します。
POINT
瓶供給・充填
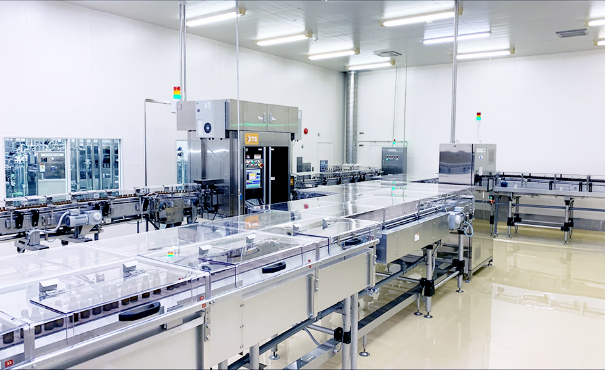
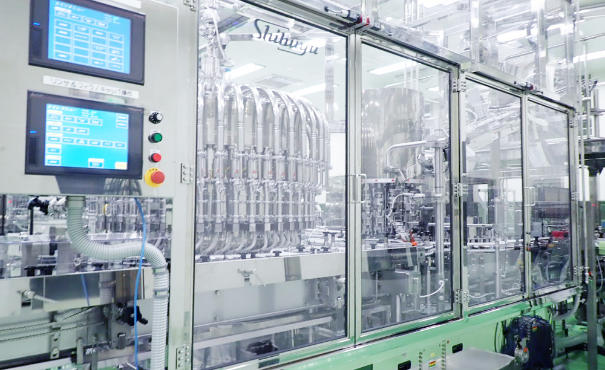
薬液を充填する硝子瓶はバルクデパレタイザーにより搬送コンベヤに供給され、瓶口天面検査装置にて全数検査を実施して充填工程に搬送されます。
調製済み薬液は瞬間殺菌装置により殺菌処理され、ろ過フィルターにて異物除去後にろ過薬液保管タンクに送られます。
薬液を充填する硝子瓶は、ロータリーリンサで内・外面を精製水で洗浄後に充填設備に搬送され、ウェイトフィラーにて全数質量を計量して充填後、キャッパーでUV殺菌されたキャップを施栓します。
調製済み薬液は瞬間殺菌装置により殺菌処理され、ろ過フィルターにて異物除去後にろ過薬液保管タンクに送られます。
薬液を充填する硝子瓶は、ロータリーリンサで内・外面を精製水で洗浄後に充填設備に搬送され、ウェイトフィラーにて全数質量を計量して充填後、キャッパーでUV殺菌されたキャップを施栓します。
POINT
殺菌/異物検査
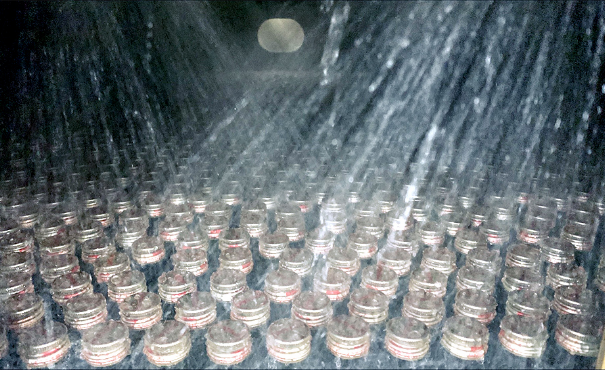
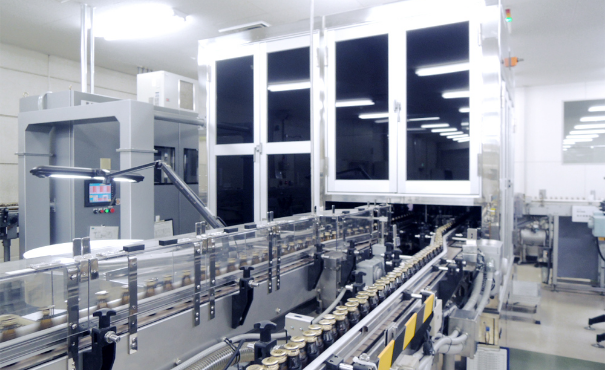
充填済み品は品目により、パストライザーにて温水シャワーによる瓶内部薬液の低温殺菌処理を行います。
殺菌済み品は、実瓶(異物)検査機により液中の浮遊性異物検査、及び瓶とキャップの外観状態を全数検査します。
殺菌済み品は、実瓶(異物)検査機により液中の浮遊性異物検査、及び瓶とキャップの外観状態を全数検査します。
POINT
包装(ラベル貼付)
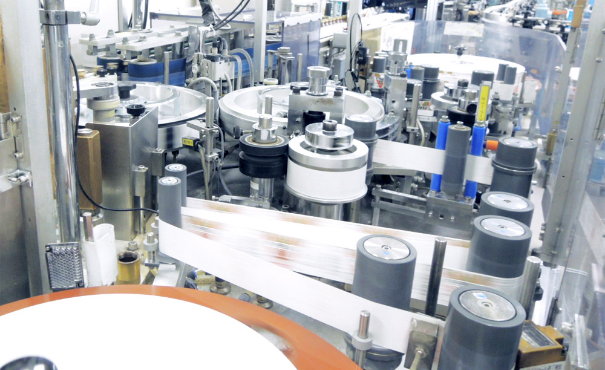
殺菌済み瓶に製造番号と使用期限を印字し、印字状態が適切であることを画像処理で検査後にラベルを貼付します。
その後、貼付されたラベルの貼付状態を画像処理で検査し、良品判定した製品のみを包装機に搬送します。
その後、貼付されたラベルの貼付状態を画像処理で検査し、良品判定した製品のみを包装機に搬送します。
POINT
包装(組箱、シュリンク、マルチパック)
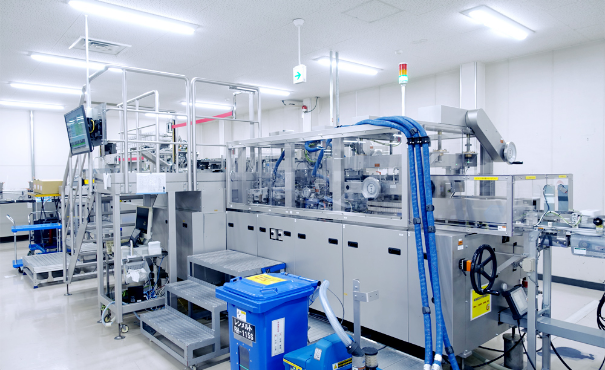
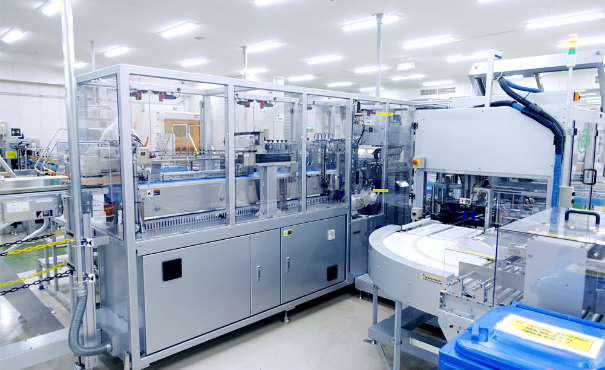
包装形態ごとに3系列の包装ラインを有しており、組箱包装は10本単位、シュリンク包装は3本単位、マルチパック包装は2本単位で個包装を行います。それぞれ個包装された製品は段ボールケースに梱包後、製造番号と使用期限を印字し画像処理で文字検査を行い、内容が適正であることを確認します。
その後、段ボールケースをウェイトチェッカーで計量して包装品に不足が無いことを確認します。段ボール梱包品はロボットパレタイザーにてパレットに自動積載され、AGVによって立体自動倉庫に自動搬送・格納されます。
その後、段ボールケースをウェイトチェッカーで計量して包装品に不足が無いことを確認します。段ボール梱包品はロボットパレタイザーにてパレットに自動積載され、AGVによって立体自動倉庫に自動搬送・格納されます。
POINT